Table of Content
Make sure you anchor your elbows onto your knees or upper legs as you do this. Make a hole in the center of the clay, then push your hand into the base, while keeping the wheel in motion. Make sure you leave enough clay at the base so you don’t push through the bottom of your pot.
You can read our blog onCan I Put A Clearcoat On Top Of Lacquer Paint? You can learn more by reading our blog,How Does The Firing Temperature Affect Ceramics Production? An advantage of a gas kiln is its soft flame that can usually be controlled.
Do You Have to Glaze Pottery
You are the artist, and only you can know what is best for the particular piece. Pottery glaze also comes in a variety of colors, so you can mix and match them to create different effects. You can also layer glazes to create a cool drippy flowing pattern. This will create a consistent pattern on your pottery. Another way to add texture is to carve designs into the clay.
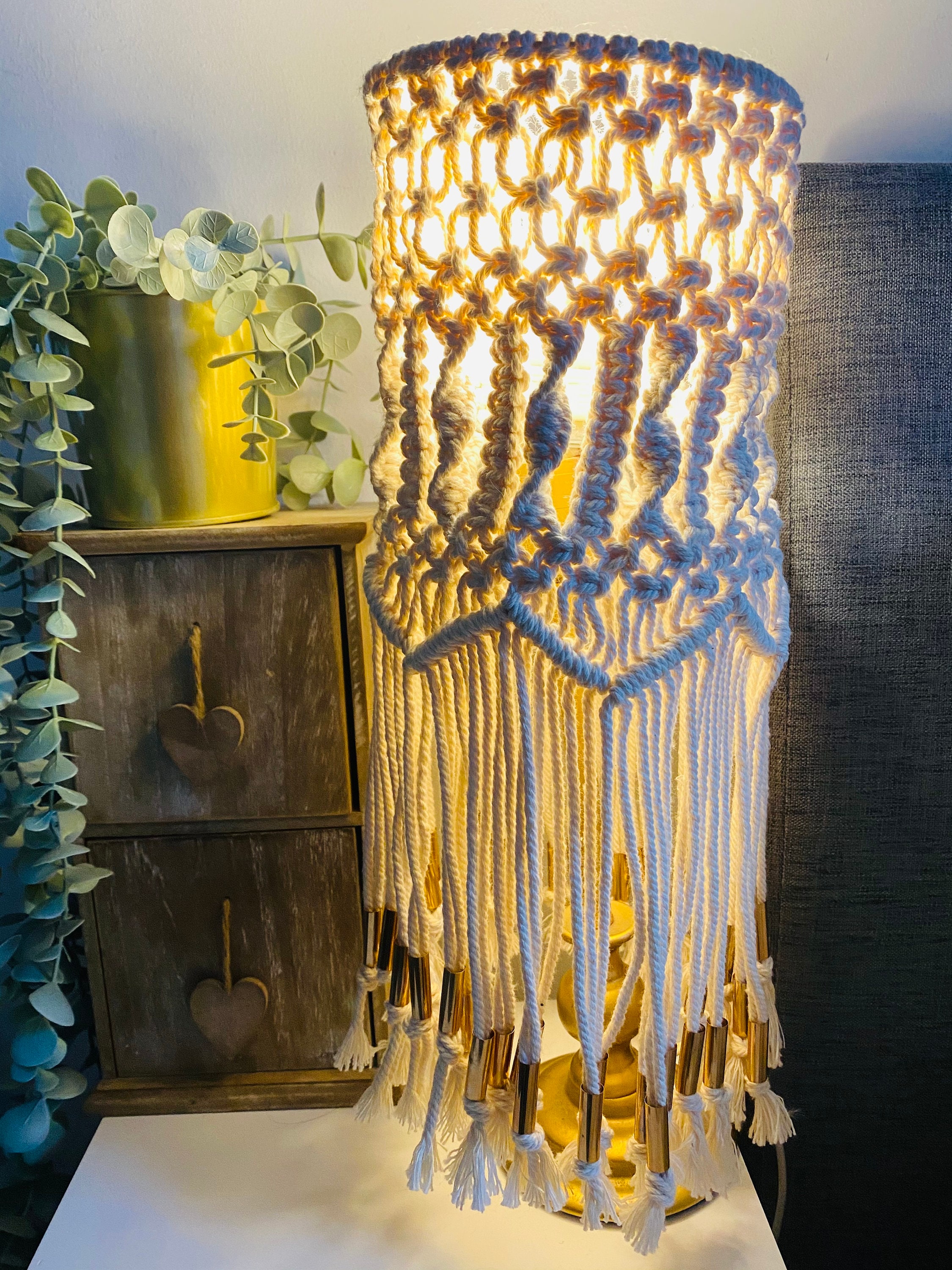
While glazing can be a long and involved process, it is not too hard to learn, and results will improve with practice. If you don't have access to a kiln, try to find one before you begin, as described within the Firing section below. But the clay must be fired first because the clay would be too fragile.
Craft Smart Natural Air-Dry Clay Review
Different materials such as copper wire, salt, and banana skin can create interesting patterns on the pottery surface. Once the fire is established, the burning pit can be covered over to keep the heat in. It can be covered with a piece of metal or some earth. The hot pottery is then placed on a bed of combustible material and covered over with a metal container. Combustible material might be straw, paper, sawdust, or something similar. As a rule, it’s best to use a glaze that matures at around the same temperature that your clay matures.
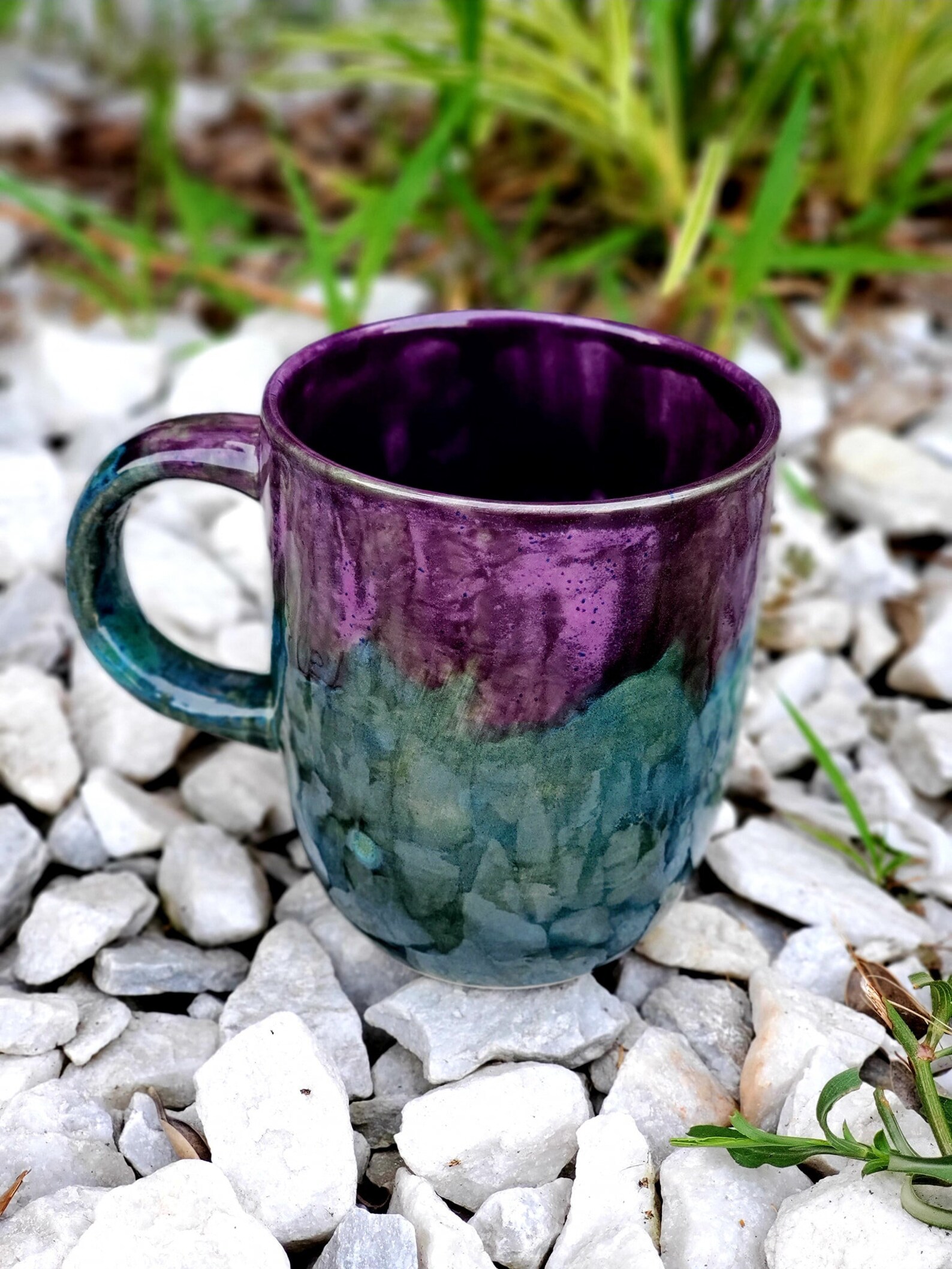
Ceramics glazes contain silica, which requires high temperatures to melt at 1800 degrees Fahrenheit and above. While home ovens cannot reach the temperatures for a silica glaze to melt, you can use alternative methods to decorate the surface of your pottery. There are paint-on enamels that fire at 300 degrees Fahrenheit. Glazed pottery will not be waterproof or food-safe unless it is fired at a high temperature in a kiln. Before you glaze pottery, fire it in a kiln so it's hard when you put the glaze on it. Next, stir a pre-mixed under-glaze thoroughly and apply it the object with a brush, letting it dry after each layer if you're using multiple colors.
Ceramic Ornaments
The glaze will make the pottery tougher and more resistant to breakage and damage. Your art will look a lot more finished and polished with a glaze on top of it. Applying Clear Glaze over your Underglaze can provide a smooth, shiny surface that is easy to clean. You can also use stamps or stencils to create patterns on your pottery. Finally, you can press things like leaves into your Clay to create a one-of-a-kind design. Overall, colored clay is a great alternative to glazing and can provide beautiful results.
Here are 9 Pottery Glazing Techniques for you to choose from. The most popular way to glaze for beginners and hobby potters is Brush glazing. And the popular way to apply for production potters is Dip Glazing. Another alternative would be to glaze your pieces at home and rent kiln space at a pottery studio in your area.
In this article, we’ll tell you everything you need to buy to start making pottery at home. The cone system measures the heat of the kiln and the length of firing. Cones are essential when firing to know when your kiln has reached the necessary temperature and to ensure the kiln is heated evenly. Each cone has a number assigned to it corresponding to a specific temperature range. For example, cone 03 indicates a temperature range of about 1,960 to 1,987 degrees Fahrenheit. We spray a PU topcoat on top of our lacquer products.
Many of the factories we work with in Asia will use a gas kiln for their production. The firing of the kiln has specific segments, and some segments of the firing process will heat up faster than others. A firing schedule is like a timetable or schedule; the kiln will increase in temperature at a specific rate. It is worth every second, and every penny, to do this.
When clay has matured, it has reached its optimal strength and density. Earthenware clays like terracotta mature at a lower temperature than stoneware clays. Buying bisque ware can be a sensible choice if your main interest is decorating pottery. However, if you want to learn about how to make your pots and fire them, then this is entirely possible too.
And eventually on the top of the pile carefully add some larger pieces of wood. It’s usual to have quite a few pots crack or break when bisque firing in a pit. The pots are less likely to break if their walls are of an even thickness. It’s best if your walls are just under half an inch thick or less, if possible.
So ideally you should apply the glaze with a larger brush that will hold quite a bit of glaze. However, if you want to use your pottery for food and drink you need to use a ceramic glaze. You can also use spray stains that are designed for craft purposes, and for porous surfaces. A good example is this range of distress spray stains by Tim Holtz.
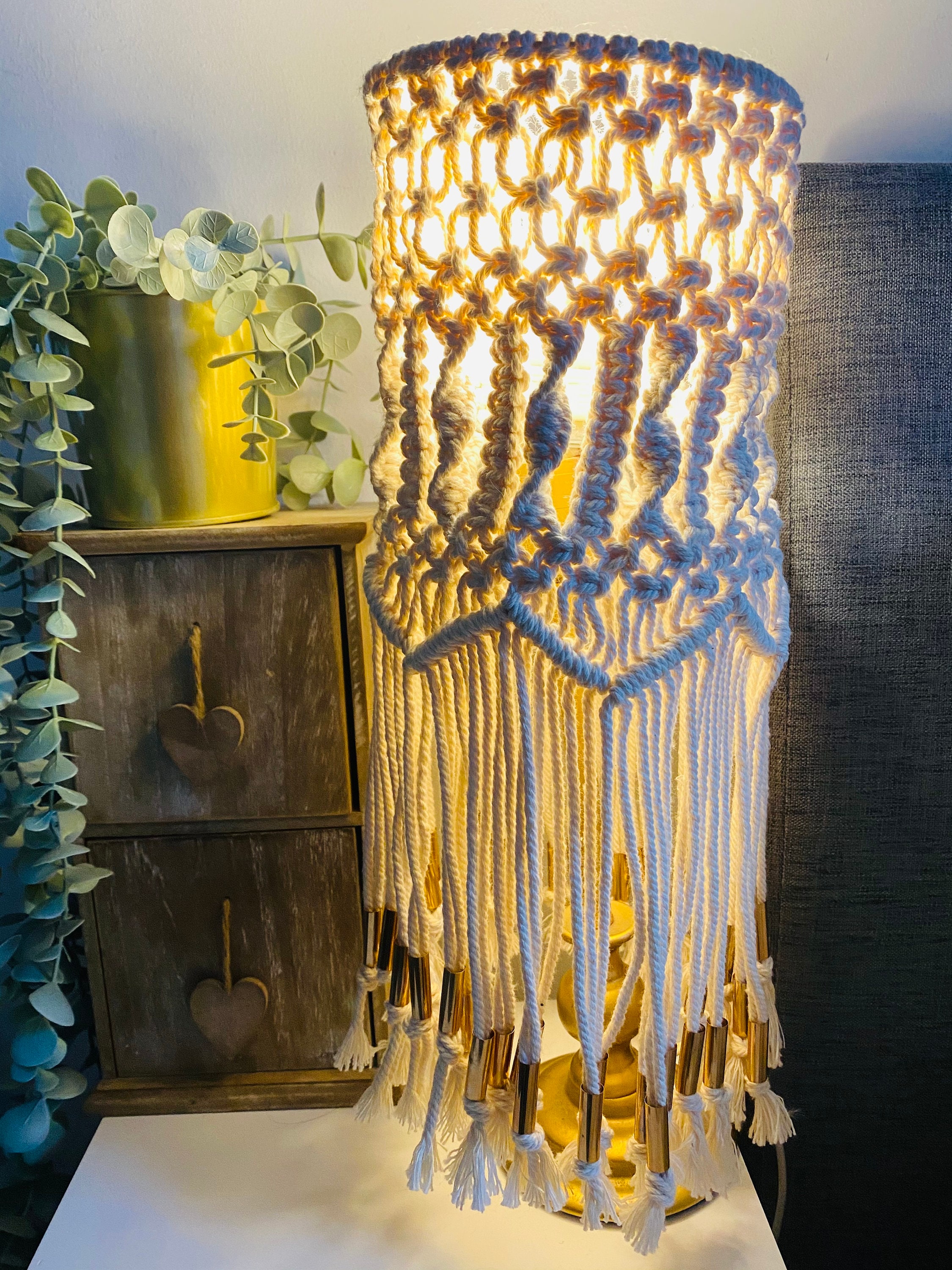
As mentioned in this article, there are an array of options available, and whatever method you opt for, a stunning glaze finish is easily achievable. Ferric chloride can then be painted carefully onto parts of the pottery. Ferric chloride is very corrosive and needs to be handled with extreme care. The updraft system gives you a bit of control over the temperature of the kiln.
No comments:
Post a Comment